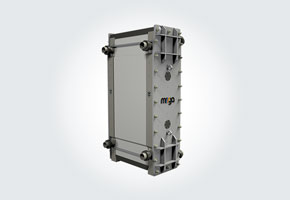
EDR stack – RALEX® EDR-IF/250
EDR-IF is an advanced EDR stack developed for high salinity water treatment in industrial applications as RO brine concentration, pre-concentration before evaporation, ZLD applications, and treatment of different types of industrial waste waters. EDR-IF provides up to 40 % higher performance compared to current EDR stacks in the market. This brings up to a 30 % layout reduction as well as a significant cost reduction. The robust design guarantees zero internal and external leakages and highly reduced downtime.